Chromatic Echoes: Restoring the Original Finishes on Antique Clock Cases
There's a profound beauty in holding a piece of history. An antique clock isn't just a time-telling device; it's a vessel, carrying within its wooden case the whispers of generations past. The finish—that carefully applied layer of varnish, paint, or the natural patina of age—is more than just aesthetics; it's a visual diary of its journey. As a clock restorer, my greatest satisfaction isn’t merely getting the mechanism ticking again, but bringing back the story held within that finish. It’s a responsibility, a privilege, and an exercise in deep respect for the original craftsman.
I remember the first clock I ever truly attempted a finish restoration on. It was a small, inlaid mahogany mantel clock from the late 1880s. The original finish was long gone, stripped away by years of neglect and ill-advised cleaning attempts. The wood itself felt lifeless, stripped of its inherent character. It felt wrong to simply apply a fresh coat of polyurethane. I wanted to understand, to honor, what had been lost. That’s when I started to learn the language of finishes—the subtle clues they left behind, the secrets they held.
Identifying the Original Finish: A Detective’s Work
Restoration isn’t about imposing your vision; it's about revealing what's already there. Identifying the original finish is the crucial first step. This isn’t always straightforward. Layers of later finishes can obscure the original, and the passage of time alters materials in unpredictable ways. There's no single, foolproof method, but careful observation and some simple tests are key.
First, look closely. Is the finish glossy or matte? Does it appear to be varnish, shellac, or paint? Varnish tends to produce a hard, durable, and often glossy surface. Shellac is softer and more pliable, often with a warm, amber tone. Paint, of course, provides complete coverage and can be matte or glossy.
A heat test (using a warm, not hot, cloth) can sometimes provide clues. Shellac will usually “tack up” slightly when warmed, while varnish tends to remain more stable. However, this isn't definitive, as some varnishes can also react similarly. Solubility tests with solvents like denatured alcohol can also be revealing, but proceed with extreme caution. Always test in an inconspicuous area first!
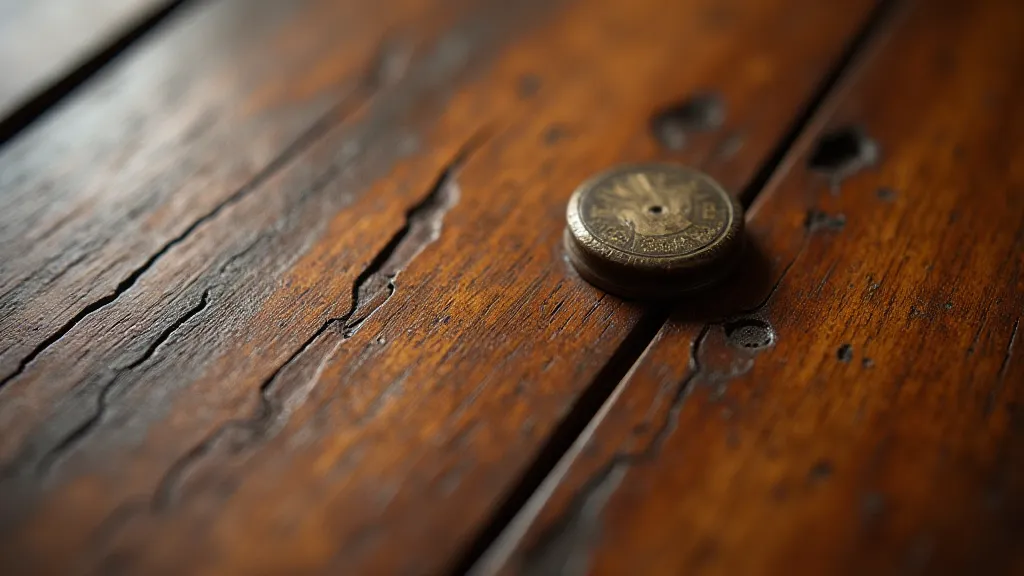
The Palette of Antique Finishes: Varnish, Paint, and Patina
The finishes used on antique clock cases varied widely depending on the era, region, and the clock’s intended market. In the 18th and early 19th centuries, shellac was the dominant choice, prized for its ease of application and beautiful, amber tone. As the 19th century progressed, varnishes, often based on natural resins like amber or copal, became more common, offering increased durability and a wider range of colors. The design and construction of these clocks reflects not just functionality, but also a deep understanding of materials and aesthetics – an element that extends beyond just the mechanics and into the larger story of time itself. You can learn more about the symbolic weight of time reflected in antique clock design here.
Painted clock cases were frequently found, especially on more affordable models. These might be a simple, opaque color or feature intricate hand-painted details. The colors themselves offer clues about the clock’s age and origin. Muted greens, browns, and creams were common in the Victorian era, while brighter, more vibrant colors became popular in the Art Nouveau and Arts & Crafts periods.
Then there's the patina—the natural aging process that creates a unique character all its own. This isn't something to be replicated; it's something to be cherished. The interplay of light, shadow, and the subtle variations in color that develop over decades are simply irreplaceable. Preserving the patina is often the most respectful approach.
The Gentle Art of Restoration: Stripping, Repair, and Re-sealing
If the original finish is beyond repair—heavily damaged, crazed, or obscured by layers of incompatible finishes—careful stripping is often necessary. Chemical strippers should be used with extreme caution, prioritizing those that are less aggressive and readily biodegradable. Mechanical stripping, using hand tools like scrapers and sandpaper, is often a safer, albeit more time-consuming, option.
Once the old finish is removed, any damage to the wood itself must be addressed. Chips, cracks, and gouges should be carefully filled and sanded smooth. The goal isn’t to make the wood look perfect, but to create a stable foundation for the new finish.
When re-sealing, the choice of finish is critical. For a shellac finish, a clear shellac is the obvious choice. For a varnish finish, a compatible varnish (nitrocellulose or a more modern blend) is essential. Modern polyurethane finishes should generally be avoided on antique clocks, as they are incompatible with traditional finishes and can cause cracking and discoloration. Sometimes, the complexity of the repair process reveals deeper mysteries within the clock's construction – a “ghost in the gears,” if you will. If you’re intrigued by the challenges of clock repair, you might find this article insightful.
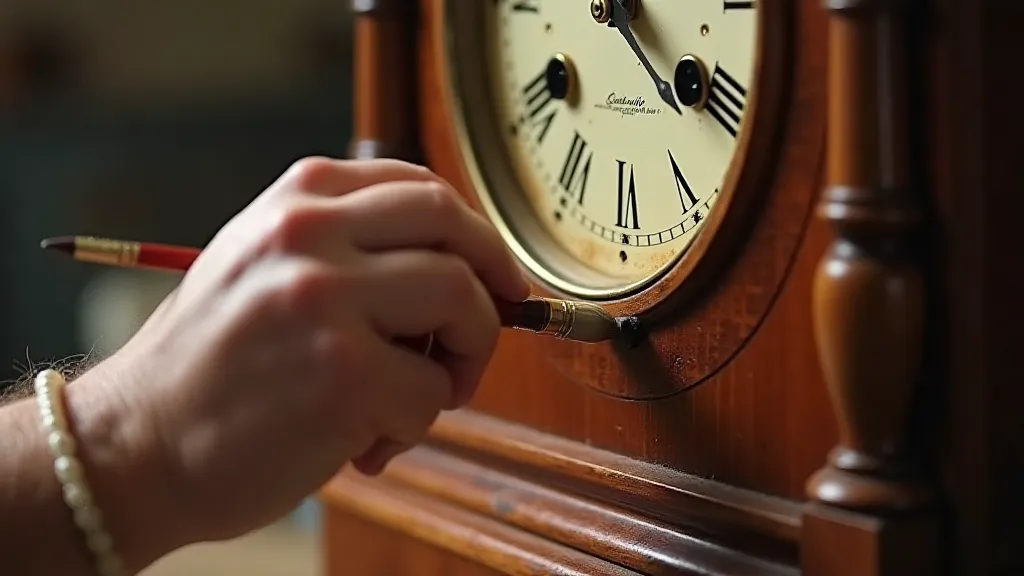
Protecting the Restoration: Long-Term Care
A beautiful restoration is only as good as its ongoing care. Avoid direct sunlight and excessive humidity, which can damage both the wood and the finish. Dust regularly with a soft, dry cloth. Avoid harsh cleaning chemicals, which can strip away the finish and dull the luster.
Waxing can provide an extra layer of protection and enhance the beauty of the finish. Use a high-quality furniture wax and apply it sparingly, following the grain of the wood. Buff to a soft sheen with a clean cloth.
Beyond Mechanics: The Artistry of the Details
The meticulous attention to detail in antique clocks extends far beyond the movement itself. Even the clock hands, so often overlooked, are miniature works of art, reflecting the prevailing design aesthetics of their time. Interested in exploring the artistry of these intricate details? You can learn more here.
The Weight of History & Preservation
The process of restoring a clock is not merely a technical exercise; it’s a form of preserving history and honoring the craftsmanship of generations past. Ensuring the longevity of these timepieces requires more than just technical expertise – it demands a deep respect for the original materials and construction techniques. Sometimes, the original parts are missing or broken, leaving restorers to grapple with the challenge of replacing them. Dealing with these challenges, such as missing weights, is a common hurdle in the clock restoration process. For those interested in understanding this specific aspect of restoration, this article provides a detailed exploration.
Beyond Mechanics: The Emotional Connection
Restoring antique clocks isn’t just about fixing mechanisms; it’s about preserving history, honoring craftsmanship, and connecting with the past. It’s a humbling process, recognizing that you’re not creating something new, but rather revealing something that was already beautiful. Each clock tells a story, and the finish is a vital part of that narrative.
I recently restored a grandfather clock that had been in a family for over a century. The original owner had carefully documented its history, including the date it was purchased and the repairs it had undergone. It was an honor to be entrusted with its care. Seeing the joy on the family’s faces when the clock was returned to its former glory—that’s the true reward.
The quiet ticking of an antique clock is more than just the sound of time passing; it's the echo of lives lived, of memories cherished. And by restoring the original finishes, we help to keep those echoes alive.
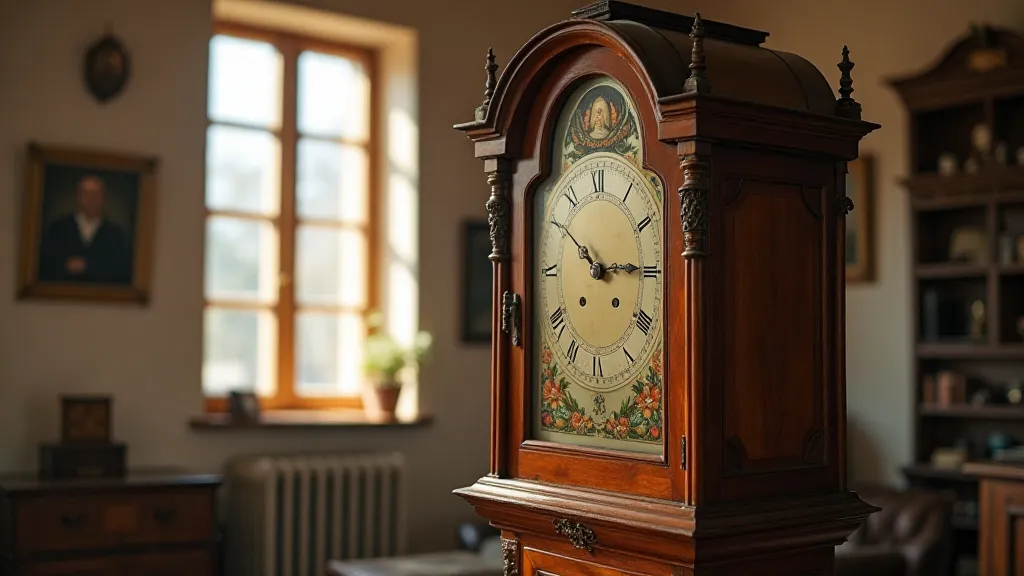